Often the terminology of engineering professionals can be highly technical and confusing. The use of terms like “Quality Assurance” and “Quality Control” is not overly technical. However, misuse can lead to serious impacts on efficient communication and the conveyance of expectations. Clarifying the terms you use is important both in-house and in your relationship with clients.
Definitions
According to Merriam-Webster Quality Control was first used in 1935 and defines the noun as, “an aggregate of activities (such as design analysis and inspection for defects) designed to ensure adequate quality, especially in manufactured products.“
Alternatively, they define Quality Assurance as, “a program for the systematic monitoring and evaluation of the various aspects of a project, service, or facility to ensure that standards of quality are being met.” This term is much newer with the first identified use in 1973.
The Management’s Strategy – Quality Assurance
In most cases and consistent with Merriam-Webster’s definition, Quality Assurance is commonly used to define the management approach. It is the foundation that establishes the expectations through policies and procedures or guidelines. These can be written or unwritten depending on the size and type of work performed by your firm. Either way, the goal is to convey to staff what the leadership team expects.
Establishing standards, monitoring their implementation, and recognizing the evolution and need to make improvements all contribute to a firm’s ability to invoke confidence in the work and deliverables they produce. From a Project Management perspective, the expectations mandate a project manager’s minimum performance standards. For corporate leadership, the mandate assists in holding project managers and project engineers accountable for the work being performed.
Executing the Expectations – Quality Control
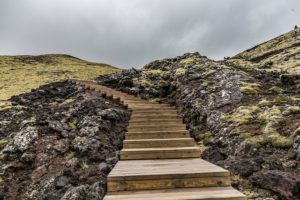
Continuing this approach, Quality Control can be seen as the processes applied to each project and specific deliverables. This includes the review for errors but also verification that the firm is putting its best foot forward. You want to make sure you meet the expectations of each stakeholder. At the end of the day, the controls put into action are designed and meant to reduce mistakes. This in turn reduces the risk each individual project presents.
It is important to recognize that Quality Control will be different for each project, each firm, and ultimately each engineer who’s in responsible charge of each unique engineering project. Each of us has followed a different path and have a diverse range of unmatched and unique experience. Every one of these experiences weighs into the decisions and choices we make while performing a quality review. Remember, a negative experience on one project can benefit all of the subsequent projects you work on.
Firm-Specific Terminology
While I have described a method for applying these definitions to your system, I must stress that the terminology used by you and your individual firm is specific to YOU. I worked with a firm that flipped the terminology upside down. Let me explain:
They applied Quality Controls as the Standards, controlling the expectations and establishing the minimum requirements for review on each project deliverable. The approach uses the authority and connotation of the word CONTROL, in their case, the LAW. Alternatively, they applied Quality Assurance as the ACTION. It ensures that reviews are being performed effectively. They knew they were being applied across the board on each and every project.
While this in fact the opposite terminology to what I described above, this is clearly and effectively communicated among their staff and clients. The point is, that the use of terminology applied to their specific scenario is not wrong!
At the same time, you want to consider not using Quality Control or Quality Assurance at all. Perhaps a program with terms like Quality Management (Assurance) and Project Performance Reviews (Control) would be more appropriate for your needs. Maybe you want to apply a broader stroke of scrutiny on the finished product with aspects of cost-benefit analysis, documentation of changes, and consideration for manhours spent to reach different project milestones. Perhaps terms like quality control are too narrow and don’t achieve the desired performance objectives for project deliverables. Not trying to reinvent your system, but simply offering a different perspective.
A Two-Part Quality Management Program
In the case of the use of the ‘different’ terminology, make a decision and stand by it. I encourage everyone to apply a consistent two-part quality management approach. One part is the establishment of the routines and the second is the implementation. Think of it as policy and procedure. Policies establish what you are going to do while procedures describe how you are going to do it.
You can call your system and your program whatever you want but you are only allowed to do that if you have clearly defined the terms and the users understand the meaning!
If this resonates with you, let’s continue the conversation! Connect with me on LinkedIn.